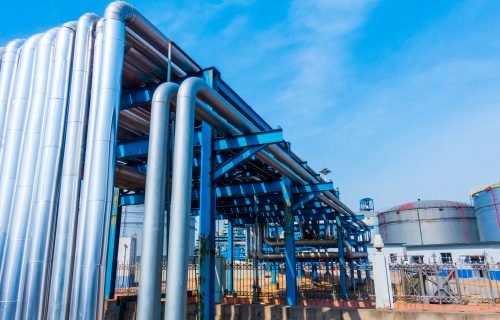
The Pikotek PGE is a non-critical service gasket designed for electrical flange isolation and/or general sealing applications. This gasket is suitable for use in raised-face flanges up to ANSI class 600 (or equivalent) and is excellent for isolating flanges made of dissimilar metals or where prevention of flange face corrosion is desired. The design of the Pikotek PGE gasket incorporates patented overlapping and offsetting seal grooves. The purpose of this design is to break each layer of laminate within the gasket itself thereby creating a barrier through which fluid and/or gas cannot migrate. The sealing element can be any elastomeric material as well as more sophisticated Spring-Energized Teflon lip seals. As a result of this advanced gasket design, maintenance free flange isolation and flange face corrosion mitigation are achieved economically.
The PGE retainer is constructed of very rigid Glass-Reinforced Epoxy (GRE) laminates, which exhibit excellent dielectric strength, high compressive strength and superior sealing characteristics.
Benefits and Advantages of PGE Flange Insulating Sets:
Here is the value we bring to you
Our decades of hands-on field experience from unconventional environments to compliance and safety, allows us to understand what you need down to the smallest detail.